Número: 224388
LOS SECRETOS DEL ALUMINIO
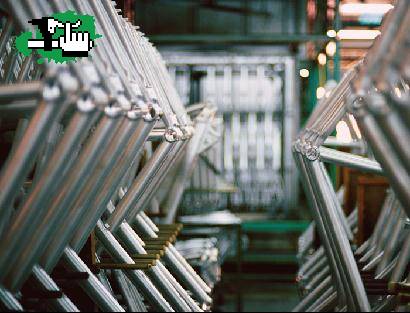
7075, 6061, forjado, mecanizado, CNC, tratamiento térmico... el aluminio es una fuente de misterios que debemos desvelar...
La principal característica del aluminio es su ligereza. Si a esto le sumamos unas propiedades mecánicas moderadamente buenas, se convierte en el mejor metal para aplicaciones estructurales en las que el peso del elemento es crítico. Sirva como ejemplo que entre el 75 y el 80% de un avión comercial esta hecho de aluminio. Además, ¿a quien no le gusta tener una bici ligera?
El aluminio es un metal abundante, el más abundante en la corteza terrestre. La producción de este material desde la mena (materia prima mineral) consume una gran cantidad de energía, pero su producción procedente de reciclado es baratísima, y no se degrada en el proceso por muchas veces que se repita. Por otro lado, no tiene una dureza muy elevada, lo que hace que sea fácil procesarlo industrialmente, conformarlo en tubos, cortarlo, estirarlo, doblarlo o mecanizarlo. Si a esto le añadimos, que la temperatura necesaria para su fusión es baja, y por lo tanto, los tratamientos térmicos que requiere y su conformado en caliente consumen poca energía, el aluminio se convierte en un material con unas propiedades realmente envidiables para cualquier tipo de proceso industrial.
Y tiene otra ventaja fundamental: el aluminio no se corroe. Se forma un óxido en su superficie que protege al resto del metal de la oxidación, y esto no es perjudicial para las propiedades del metal en la mayoría de aplicaciones.
TRÁTAME CON DELICADEZA
Después de analizar las fantásticas propiedades de este material, podríamos preguntarnos por qué el aluminio no había triunfado hasta estas últimas décadas en la industria de la bici. Los inicios del aluminio en la fabricación de cuadros para bicicletas no fueron muy esperanzadores, principalmente por que no se diseñó teniendo en cuenta sus peculiaridades:
Soldabilidad: para conseguir una soldadura de calidad, es necesario un proceso muy cuidadoso y controlado, pero no todas las aleaciones se pueden soldar. De hecho, las aleaciones tradicionalmente soldables de aluminio no son las más resistentes. Los más veteranos recordaréis aquellos cuadros de aluminio pegado.
Ductilidad: es la capacidad del material para soportar deformaciones sin romperse, esta propiedad es el "colchón de emergencia" a la hora de llevar a la realidad los cálculos realizados sobre papel. Resistencia a fatiga del aluminio, aunque es buena, presenta dos inconvenientes básicos. El primero es que no existe un límite de fatiga para vida infinita. Esto quiere decir que si aplicamos un esfuerzo en una pieza de aluminio, durante un número suficiente de veces (puede llegar a cientos de millones), la pieza termina fallando siempre, por bajo que sea el esfuerzo. El otro inconveniente es la incomodidad. Su buena respuesta a la fatiga empeora mucho cuando se ve obligado a soportar deformaciones que serían normales para acero o titanio, por lo que el ingeniero se ve obligado a limitar al máximo las deformaciones y a diseñar una estructura más rígida que si lo hiciese con otro material, para conseguir fabricar algo verdaderamente duradero.
TODO TIENE SOLUCIÓN
Veamos cómo se han ido solventando los problemas desde los primeros y poco halagüeños inicios:
Soldadura TIG
Es uno de los procesos de soldadura que proporcionan mejor calidad al producto acabado, pero es uno de los más difíciles y exigentes de ejecutar. Los soldadores cualificados para soldar aluminio con este proceso son trabajadores muy especializados, y podrán soldar de 12 a 14 cuadros por turno. Este proceso no es nuevo, pero ha presentado tradicionalmente bastantes dificultades a su automatización, sobre todo a la hora de soldar curvas de difícil definición como son las líneas que unen los tubos de un cuadro. Esto es un avance muy reciente y probablemente sea la clave de la popularización y disminución de precio de este tipo de cuadros.
Diseño Oversize
Inventado a principios de los '80 (Cannondale fue pionera), viene a adaptar el menor módulo de elasticidad y la menor tolerancia a deformaciones del aluminio, a la fabricación de cuadros de bicicleta. Este aspecto es crítico cuando deseamos un cuadro resistente a la fatiga.
Conificado
Se creó para reforzar los extremos de los tubos que soportan la soldadura, en los que se producía un debilitamiento importante. Esto ha resultado tener un efecto asociado muy importante: el conificado refuerza las zonas en las que los esfuerzos son mayores, los extremos. Las primeras series de aluminio conificado se fabricaron a mediados de los '90, venciendo definitivamente la batalla del peso, que hasta ese momento tenía con los cuadros de acero de calidad.
Hidroformado
Este proceso ha sido quizás el que, junto con la automatización de la soldadura, más ha influido para que los cuadros de aluminio se hayan impuesto por encima de los de otros materiales, ya que ha permitido dotar a los cuadros de formas muy variadas en el mismo tubo.
Punteras de cambio desmontables
Los veteranos recordareis las estilizadas punteras de cambio de las bicis de acero, en las que con una cantidad escasa de material se conseguía la resistencia adecuada para que realizase su función. Con el aluminio había un problema: su resistencia total es más baja, y la cantidad de material que se podía poner en ese punto no proporcionaba una buena solución. El ingenio acudió al rescate: se inventaron las punteras reemplazables y asunto resuelto.
ME DEJO LLEVAR
Fabricar una estructura tubular de aluminio resulta más sencillo que hacerla de acero o titanio, porque la facilidad para cortar, mecanizar o doblar es mucho mayor con aluminio, consumiendo por tanto, menos energía y menos tiempo en las operaciones necesarias para dejar los tubos listos para soldar. La primera razón son las menores propiedades mecánicas, sobre todo en el ámbito de resistencia y dureza. La resistencia tiene influencia mayormente en los procesos de doblado para conformar vainas y tirantes. La menor dureza, ayuda a la hora de mecanizar y roscar, siendo más fácil y rápido. La segunda razón es su menor punto de fusión, esto permite dos importantes ventajas: la primera es que se consume menos energía al cortarlo por láser, que es más barato y más preciso; la segunda es que la energía necesaria para su conformado en caliente, y sus tratamientos térmicos, es mucho más baja porque las temperaturas de los hornos son bastante menores.
CUIDADITO CONMIGO
En condiciones normales las zonas más débiles de un cuadro son las soldaduras y las zonas cercanas, por tanto no sirve de nada obsesionarse con la resistencia del material empleado si luego el proceso de soldadura y posterior tratamiento térmico no se hace adecuadamente. Soldar aluminio es algo bastante delicado, que presenta las siguientes dificultades:
-No todas las aleaciones de aluminio son soldables, de hecho las soldables son una minoría. Pero además de ser soldable por sí misma, se necesita que sea tratable térmicamente, para aliviar tensiones al final del proceso completo de soldadura.
-El debilitamiento asociado a la soldadura del aluminio es grande.
La primera razón por la que ocurre esto es porque la conductividad térmica del aluminio es muy alta y la zona afectada por el calor de la soldadura, que es la que se debilita, se amplía. La segunda es que, aunque la temperatura de fusión de aluminio es más baja, el espesor de los tubos es mayor, con lo que la cantidad de energía que se aporta estará en valores similares a la aportada para un cuadro de acero o titanio, pero con una zona afectada más amplia.
-El gran riesgo de las soldaduras de aluminio son las inclusiones porosas, esto son burbujas de gas que se quedan atrapadas dentro del cordón cuando el metal solidifica. Hemos dicho que tiene una conductividad térmica alta, se enfría rápido, es poco denso, por lo que las burbujas no escapan tan rápidamente como en otros metales mas pesados. Es terriblemente fácil que se queden atrapadas.
-Enfriamiento homogéneo, también hemos dicho que se enfría muy rápido. Uno de los grandes riesgos a la hora de soldar es que las zonas cercanas se enfríen de diferente manera, una muy lentamente y otra muy rápidamente, esto produce tensiones internas que debilitan el material. Esto se produce cuando se sueldan dos zonas con distintos espesores, cuando un refuerzo no está bien pensado, cuando hay esquinas que se pueden enfriar más rápido o cuando un cuadro está sometido a una corriente de aire. Muchos sabréis que un cuadro de acero lo reparan en cualquier parte, pero uno de aluminio es otra cosa, aquí hemos visto algunas razones.
EL TRATAMIENTO TÉRMICO
Acabamos de decir que el material con el que esté fabricado el cuadro tiene que ser tratable térmicamente, para aliviar tensiones y restaurar las propiedades de la aleación en las zonas afectadas por el calor de la soldadura. Estas tensiones se crean en el cuadro básicamente por dos procesos:
-El ciclo térmico de la soldadura. Soldar un material implica introducir, en la zona afectada por el calor, un montón de modificaciones metalúrgicas en el material de base, que introducen tensiones residuales debidas al ciclo de calentamiento-enfriamiento. Hemos dicho que la zona que se somete a este proceso es muy amplia. Este ciclo también hace que en las cercanías de la soldadura varíe la composición de la aleación del metal de base, porque la solubilidad del metal fundido es mucho mayor que la de otros estados, y esto proporciona un reparto "desigual" de los elementos aleantes, por lo que hay que intentar restablecer esa homogeneidad en la medida de lo posible.
-Nivel de embridamiento. Un cuadro de bicicleta o sus partes móviles, si es de suspensión, van enteramente soldados. Esto implica que una parte -un tubo, una puntera- no se puede mover sin desplazar al resto, tiene lo que se denomina movimiento impedido, por lo que el nivel de tensiones remanentes después de la soldadura aumenta. Esta pérdida de propiedades, a diferencia de la otra, es la que una soldadura induce tanto en si misma como en las demás si el desplazamiento de los elementos que une esta restringido de algún modo, como lo es en un cuadro. Además, en un cuadro los requisitos de alineación son muy severos, porque influyen drásticamente en su calidad, y en que sea "conducible" o no. La alineación se hace después de la soldadura e incrementa las tensiones por que altera el estado "natural" de la estructura al final de la soldadura, que por supuesto no es alineado.
Los tratamientos térmicos a los que se suelen someter los cuadros son: Solubilización y Endurecimiento por precipitación.
Solubilización: Es un tratamiento térmico que consiste en calentar el material en torno a los 530 ºC, el tiempo suficiente para asegurarse que la totalidad de la pieza se encuentra a esa temperatura y enfriar con rapidez en agua a no más de unos 30-35 ºC. Este tratamiento lo requieren, por ejemplo, los cuadros soldados de la serie 6061. Estas aleaciones presentan la peculiaridad de que se recomienda realizar el alineamiento del cuadro después de la solubilización, puesto que le proporciona a la aleación una resistencia moderada y una buena ductilidad, propiedades que mejoran esta operación. No se realiza tratamiento de solubilización en las aleaciones de la serie 7000.
Endurecimiento por precipitación: Es un tratamiento térmico que también se llama envejecimiento. Se realiza como operación final, previa al pintado del cuadro, cuando ya se han soldado todos los componentes y se ha realizado la alineación. Es el último paso de fabricación del cuadro propiamente dicho, varía en función de las características propias de la aleación y el tipo de estado final de templado requerido. Los famosos T-4 y T-6, un ejemplo típico de un endurecimiento por precipitación, puede durar unas 8 horas a 175º C.
LA FORMULA MÁGICA: CONIFICADO+HIDROFORMADO
Como hemos comentado, el conificado se realiza por dos razones: porque en los extremos el material se debilita como consecuencia del proceso de soldadura, y porque los tubos reciben mas esfuerzos en los extremos que en el centro. Para disminuir los efectos de la soldadura no hay mucho margen de maniobra mas allá de una ejecución cuidada; pero para asimilar los mayores esfuerzos en los extremos, aumentar el espesor no es una buena solución, sería mucho mejor poder ampliar el radio del tubo en la dirección de donde viniesen los esfuerzos de manera que los asimilase mejor. Parece lógico pensar que un tubo de mayor radio soporta más esfuerzos que uno de menor. Es aquí donde conseguir que los tubos tengan formas mas variadas aparece como una ventaja fundamental.
El conificado de los tubos se realiza con un estirado controlado del tubo. De que el conificado se realice en una o en dos fases, se obtiene un tubo doble o triple conificado, es decir, con dos o tres espesores distintos en su sección transversal. De la forma en la que se estire depende que las zonas con espesor diferente sean más o menos amplias y el cambio de espesor sea más o menos brusco.
Para cambiar la forma de los tubos hay dos procedimientos principalmente: presionándolos exteriormente con una matriz o molde que tenga la forma deseada, o expandiéndolos interiormente sellando los extremos y ejerciendo una presión hidrostática desde el interior del tubo que se adaptará a la forma que tenga la matriz exterior (hidroformado). La combinación de estos métodos de fabricación permite la adopción de casi cualquier forma para el diseño del tubo. Si estas formas se aprovechan adecuadamente, permiten adaptar al máximo las cualidades estructurales de cada uno de los tubos a las necesidades de resistencia en cada zona del cuadro, consiguiendo bajar, año tras año, el peso final del cuadro.
Por: Eduardo Mialdea
SALUDOS
PELABIKE